With the increase in the output of clean steel, the use conditions of ladle refractory materials have become worse. The temperature of molten steel increases, and the residence time of molten steel in the ladle is prolonged. The scouring of molten steel and slag on ladle refractory materials, as well as the chemical erosion of slag on ladle refractory materials, are more serious. The previous ladle refractory materials can no longer meet the needs of modern steelmaking production. For this reason, a variety of aluminum-magnesium (carbon) refractory materials for ladle have been developed one after another. During the use of aluminum-magnesium (carbon) refractory materials, A12O3 and MgO react at high temperature to form magnesium-aluminum spinel, a mineral with excellent high-temperature performance, which significantly improves the erosion resistance and spalling resistance of the refractory materials. Therefore, the use of aluminum-magnesium (carbon) refractory materials for ladle can greatly increase the service life of the ladle.
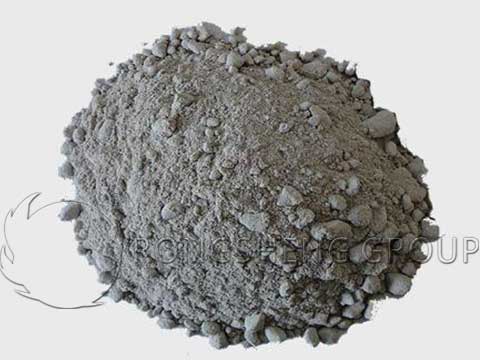
(1) Aluminum-magnesium integral ramming material. The ramming material is a kind of plasticity formulated with special high-alumina bauxite clinker as aggregate, a mixed powder of special-grade high-alumina bauxite clinker powder and sintered magnesia powder as matrix, and liquid water glass as binding agent. Good unshaped refractory material. Used on a 200t ladle in a steel plant, the service life is 5 to 7 times longer than that of clay bricks. The average service life is 85.15 times, with a maximum of 108 times, and the consumption of refractory materials per ton of steel is 2.7kg. After that, many steel mills successively used this aluminum-magnesium ladle integral ramming material in their ladles, and achieved good results.
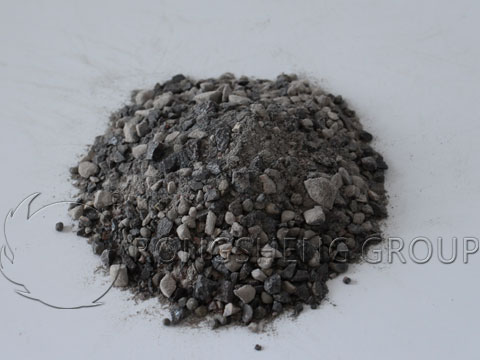
(2) Aluminum-magnesium castable. Following the aluminum-magnesium ramming material, aluminum-magnesium castables were developed using high-quality high-alumina bauxite clinker and sintered magnesia as raw materials and using liquid water glass as a binder. The castable was first promoted and applied on small ladles and achieved good results. For example, the 10t and 14t ladles of a steel plant use aluminum-magnesium castables combined with water glass, and the average ladle age is 109.7 times, which is more than 8 times that of clay brick linings. The 15t and 13t ladles of another steel plant use aluminum-magnesium castables and have a ladle life of 53 times, while the clay lining brick ladles have a ladle life of only 6 to 10 times. After that, most converters with a capacity below 30t, medium and small ladles, and ladles with a capacity below 45t adopted integral cast ladle linings. The service life of the overall cast ladle lining is mostly 40 to 60 times, and some small ladles can reach 90 times. Refractory material consumption and lining costs have been significantly reduced, achieving obvious economic benefits.
(3) Aluminum-magnesium no-burnt bricks. In addition to aluminum-magnesium ramming materials and aluminum-magnesium castables, water-glass bonded aluminum-magnesium unburned bricks have also been developed. When used on ladles, their service life is longer than traditional aluminum silicate ladle bricks. The 160T ladle uses aluminum-magnesia unburned bricks, with an average service life of 40.56 times, which is more than double that of using third-grade high-alumina bricks (lifespan of 18.5 times). In a steelmaking plant, the average service life of aluminum-magnesium unburned bricks used in a 20t ladle is 38.8 times, with a maximum of 55 times, which is more than four times the service life of clay lining bricks (9 times).
(4) Aluminum magnesium spinel castable. Alumina-based alumina-magnesium spinel castable for ladle. Since a certain proportion of pre-synthesized magnesia-aluminum spinel is added to this type of castable, the corrosion resistance and spalling resistance of the castable are greatly improved. The aluminum-magnesium castable has better performance than water-glass combination, and has achieved good results when used on various types of ladles.
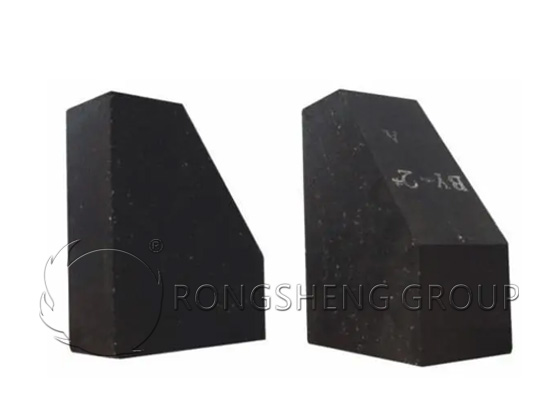
(5) Alumina-magnesia carbon bricks. In order to improve the service life of continuous casting ladles and meet the needs of the development of efficient continuous casting technology, alumina-magnesia carbon bricks for ladles were developed. Used in various types of continuous casting ladles to greatly increase the service life of the ladles. Aluminum-magnesia carbon ladle bricks are used in the 300t continuous casting ladles of steel plants. The ladle age has increased from more than 20 times when first-class high-alumina bricks were used, to more than 80 times, and up to 126 times. There is also a steel plant with a 200t full continuous casting and out-of-furnace refining ladle, using alumina-magnesium carbon bricks, with an average lifespan of 64 times and a maximum of 73 times. Many steelmaking plants, based on the actual situation of the enterprise, have successively used aluminum-magnesium-carbon ladle lining bricks, which has significantly increased the life of the ladle.
Alumina-magnesia carbon bricks are unfired products made of special-grade high-alumina bauxite clinker, fused magnesia or sintered magnesia and graphite as raw materials, and liquid phenolic resin as a binder. This product has good slag erosion resistance, strong corrosion resistance, good thermal shock resistance, low price, and is mainly used in the non-slag line parts of the ladle.
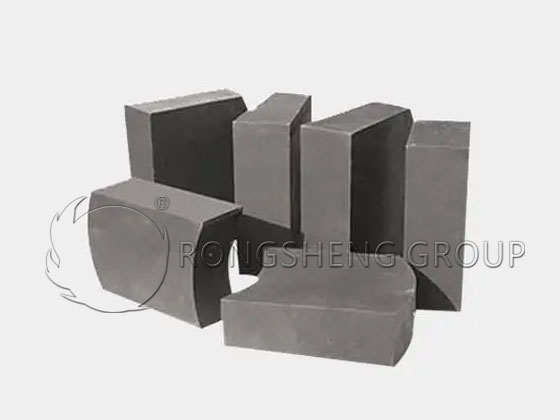
(6) Aluminum-magnesium spinel carbon bricks. On the basis of the development of alumina-magnesia carbon bricks, my country has also developed alumina-magnesia spinel carbon bricks for ladles. Alumina-magnesia spinel carbon bricks add a certain proportion of pre-synthesized magnesium-alumina spinel into the bricks, and their performance is better than that of the same grade of alumina-magnesia carbon bricks. Aluminum-magnesium spinel carbon bricks are used on 300t continuous casting ladles, with an average service life of 105 times and a maximum of 200 times. Aluminum-magnesia spinel carbon bricks are used on ladles that are fully continuously cast and refined outside the furnace. The average service life is 73.3 times, with a maximum of 82 times.
Aluminum-magnesium spinel carbon bricks are used on 90t ladles in steel plants. The service life has been increased from 20 times when using alumina-magnesia carbon bricks to 40 times, and the highest is 51 times. The development and use of alumina-magnesia spinel carbon bricks has further improved the service life of my country’s continuous casting ladles.
(7) High-grade aluminum-magnesium non-burning bricks. Carbon-containing ladle lining bricks will cause carbonization of molten steel during use, which is very detrimental to the smelting of clean steel, low carbon steel and ultra-low carbon steel. In order to meet the needs of clean steel, low carbon steel and ultra-low carbon steel smelting, high-grade aluminum-magnesium non-burning bricks and carbon-free non-burning bricks have been developed. High-grade aluminum-magnesium unburned bricks not only use high-purity raw materials, such as corundum, high-purity fused magnesia and high-purity aluminum-magnesia spinel, but also use high-performance composite binders as binders. High-grade aluminum-magnesium unburned bricks have achieved good results when used on ladles. The service life reaches or even exceeds that of carbon ladle lining bricks, while reducing the carbonization of molten steel. For example, alumina-magnesia unburned bricks are used on 100t ladles and LF refining ladles in a steel plant, and their service life is 1.5 times that of alumina-magnesia carbon bricks. In some steel plants, a 200t ladle made of aluminum-magnesium unburned bricks has a ladle life of more than 110 times, with a maximum of 128 times. The service life of the 170t continuous casting ladle reaches 119 times, which exceeds that of alumina-magnesia carbon bricks.
(8) High-grade alumina-magnesium spinel castable. High-grade aluminum-magnesium castable, used for large and medium-sized ladles. The raw materials used in high-grade aluminum-magnesium spinel castables include corundum (fused corundum, sintered corundum, etc.), high-purity fused magnesite, high-purity aluminum-magnesium spinel (fused and sintered), etc. Binders include pure calcium aluminate cement, A12O3 micropowder, high-purity SiO2 micropowder, etc. A 300-ton steel ladle in a steel plant tried high-grade aluminum-magnesium castables developed by many refractory materials factories in my country. By 2000, the average service life was 258 times. Used on a 90t LF refining ladle in a steelmaking plant, the service life is 138 times and the erosion rate is 0.62mm/time. Another steelmaking plant’s 200t continuous casting ladle uses high-grade aluminum-magnesium (spinel) castables with a service life of 150 times. Some steel plants use castable prefabricated blocks and have achieved good results. The service life of a steel ladle in a steel plant using aluminum-magnesia carbon bricks is 65 times. After switching to high-grade aluminum-magnesium spinel prefabricated blocks, the average service life increased to 118 times, and the highest was 126 times.
To extend the life of the ladle, use high-quality refractory lining materials. To choose a competent and experienced refractory material production and sales manufacturer, please contact us.
Leave Your Requirements on RS Kiln Refractory Bricks And Castable Materials! We Will Reply You In 12 Hours!: