RTO (Regenerative Thermal Oxidizer) is the abbreviation of regenerative exhaust gas treatment device, also known as regenerative waste gas incinerator, which is mainly used to remove harmful volatile organic compounds in waste gas. RTO furnace insulation belongs to the new generation of organic waste gas treatment equipment insulation. It is mainly used for various paint waste gas treatment, medical waste gas treatment, etc. In the past, horizontal torpedo tank incinerators were mostly used. With the continuous improvement of energy conservation, especially environmental protection requirements, in recent years, the insulation of regenerative waste gas incinerators has gradually moved from theoretical research to engineering practice.
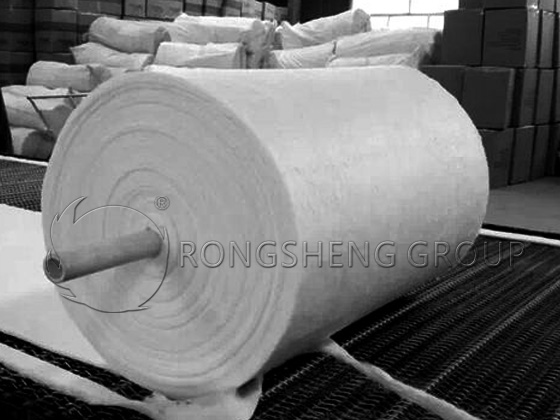
Working Principle of RTO Furnace
The conditions required for the incineration of organic volatile solvents are sufficient temperature (760℃), sufficient residence time (1.6s), and good mixing of air and solvent. At the same time, the solvent can also generate a large amount of heat when it is incinerated.
The working principle of RTO furnace is: after the organic waste gas absorbs heat and heats up in the preheating chamber, it enters the combustion chamber for high-temperature incineration (heating to 800℃), oxidizing the organic matter into carbon dioxide and water. After passing through another heat storage chamber to store heat and then discharge, the stored heat is used to preheat the newly entered organic waste gas. The direction of the air flow is changed periodically to maintain the stability of the furnace temperature.
The ceramic heat storage part consists of two or more chambers. Before the relatively clean gas after pyrolysis enters the exhaust gas treatment system or is directly discharged, each chamber needs to be purged to ensure the removal rate of VOC. This method can save fuel consumption for preheating and heating of exhaust gas.
The ceramic fiber lining of the RTO furnace uses 1260 ceramic fiber modules and 1260 ceramic fiber blankets to insulate the ceramic heat storage chamber and combustion chamber. The arrangement of the ceramic fiber folding modules adopts the “soldier column” – arranged in the forward direction along the compression size of the module. A layer of 20mm thick ceramic fiber blanket is folded in half and compressed between the rows of ceramic fiber modules, and “U”-shaped nails are used to maintain a spacing of 500-700mm and insert it into the fiber module to compensate for the possible shrinkage of the non-expanding surface of the fiber. This structure can avoid the phenomenon of “flower heart” caused by uneven expansion of the corners of the ceramic fiber module in the “parquet floor” arrangement, and achieve good insulation effect. When installing the backing layer at the top of the furnace, the quick card matching module is used for temporary fixation with bolts.
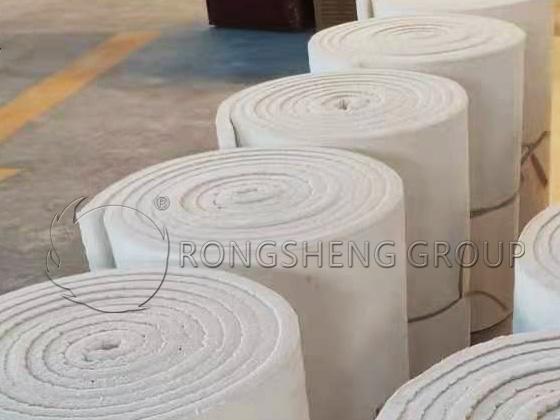
The surface of the ceramic fiber module of the hot surface of the RTO furnace ceramic fiber lining is coated with curing agent twice, which can resist water vapor and high wind speed flue gas scouring, and extend the service life of the insulation lining.
Advantages of using ceramic fiber blankets and ceramic fiber modules for RTO furnace insulation refractory materials:
- Light weight. The ceramic fiber material specially used for RTO furnace insulation is 1/30 to 1/10 of the weight of traditional refractory materials. This greatly reduces the weight load of the RTO furnace insulation structure and reduces the project cost of the RTO furnace.
- Low thermal conductivity. The thermal conductivity is lower than 0.03w/(m·k) at room temperature, with good insulation effect, which better keeps the heat in the heat storage chamber from dissipating. This reduces the addition of auxiliary fuel and reduces operating costs. After the RTO furnace is insulated with ceramic fiber lining, the surface temperature of the furnace body is low and the service life is long.
- Good thermal shock resistance. Ceramic fiber has good thermal shock resistance and can cope with the alternation of hot and cold caused by temperature changes caused by periodic replacement of the air inlet of the RTO furnace, ensuring the integrity of the furnace lining. The lightweight and high-temperature resistant ceramic fiber lining of the RTO furnace has excellent resilience. After the pre-compressed refractory module is installed and the packing tape is removed. An airtight overall refractory layer is immediately formed without the need to reserve expansion joints.
- Strong chemical stability. Ceramic fiber is an inorganic non-metallic material with extremely strong chemical stability and is not easily affected by the harsh combustion atmosphere inside the RTO furnace.
- Reduce noise pollution. Ceramic fiber blanket is an irregular porous refractory material interwoven with ultra-fine inorganic fibers, which has excellent environmental protection performance of sound reduction, noise reduction, sound absorption and emission reduction. Therefore, the combustion process of toxic waste gas in the RTO furnace is like a muffler with good performance, and the operating noise is very low, which greatly optimizes the production environment of the factory.
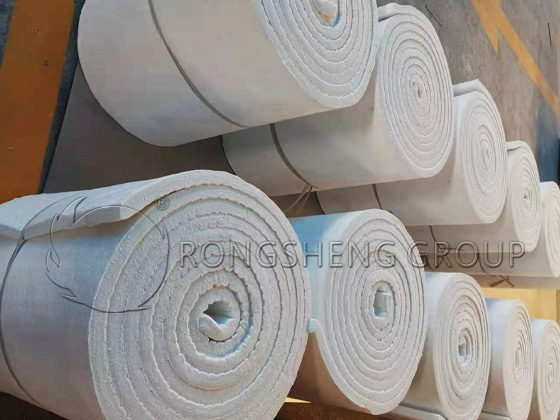
Application of Ceramic Fiber Materials Resistant to High Temperature of 1600℃ in the Insulation Industry
Since the 21st century, some large ceramic fiber material manufacturers have made major adjustments in product structure, expanding the production capacity of high-purity aluminum silicate fiber, chromium-containing fiber, zirconium-containing fiber, polycrystalline alumina fiber, and polycrystalline molybdenum fiber.
Nowadays, ceramic fiber has been maturely used in detachable flexible insulation. The new flexible detachable insulation product developed with ceramic fiber as the base material has the advantages of lightweight, high-temperature resistance, good thermal stability, low thermal conductivity, low specific heat, and resistance to mechanical vibration. Therefore, it has been widely used in machinery, metallurgy, chemical industry, petroleum, ceramics, glass, electronics, and other industries.
Rongsheng ceramic fiber insulation material products meet the diverse and personalized needs for equipment-energy-saving, thermal insulation, heat insulation, antifreeze, fire prevention, etc. Contact Rongsheng and get free samples and quotations.
Leave Your Requirements on RS Kiln Refractory Bricks And Castable Materials! We Will Reply You In 12 Hours!: