RS Kiln Refractory’s refractory lining materials are customized according to the customer’s actual working conditions. They can effectively extend the service life of the lining materials. Of course, there are different opinions in customer feedback.
Case Analysis of Overall Damage to Refractory Castables
As a manufacturer of refractory castables, Rongsheng has always been particularly attentive to product quality. This is to enable customers to effectively solve furnace lining problems and reduce production costs. However, in reality, many accidents often occur. Some time ago, a customer needed to cast an outer refractory layer for the heating furnace in his factory and purchased 2 tons of refractory castables. After buying the materials, they carried out construction and maintenance in accordance with the use of refractory castables, including supporting molds, adding water and stirring, and vibrating pouring. However, after pouring, large areas of cracks appeared less than 2 days after the furnace was opened, causing overall damage to the refractory castable prefabricated body. Then, the customer contacted us and said that our castables were useless and all exploded! The quality of the castables was not good, etc. Of course, Rongsheng manufacturers will not sit idly by when encountering problems. We will coordinate with the technical department to analyze and investigate the causes as soon as possible. We have given customers a satisfactory after-sales service.
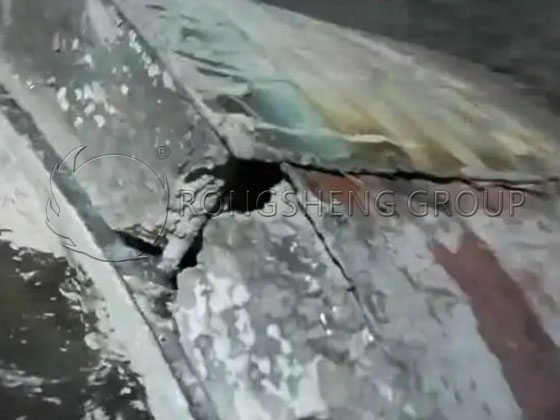
Our technical department asked the customer to take a video to analyze and find the cause of the problem. The strength of the castable after pouring has reached the initial hardness, and there are no casting defects such as segregation and bleeding on the surface of the cast body. But why is there such a big crack? By comparing multiple pictures, we observed that the problem occurred on the anchor nails connecting the furnace wall and the mold. It was found that the starting end of each crack was from the position of the anchor nail and extended vertically downward. And the crack at the anchor nail position is the largest and widest, and the smaller it is as it goes down. This shows that there was no measure to make the thermal expansion joint of the anchor nail before pouring.
Anchor nails are embedded parts that mainly support the lining of refractory castables or refractory prefabricated blocks of thermal equipment to enhance the resistance of refractory castables to static loads, thermal stress, mechanical expansion, and mechanical vibration. However, before the construction of the castable, it is necessary to consider the matching of its expansion coefficient with the castable and the influence of the expansion amount. Generally, the expansion of steel anchors is relatively large, while the expansion coefficients of refractory bricks and castables are relatively small.
Therefore, the treatment of the expansion joint on the surface of the anchor must be considered comprehensively. If the gap is too large, the anchor will separate from the castable, and it is easy to oxidize and break, and the anchoring effect will not be achieved. If it is small, it is easy to cause the castable to expand and crack. From the relationship diagram of the linear expansion coefficient, linear change rate and temperature of the castable and its internal anchor, it can be seen that: as the temperature increases, the difference in the linear expansion coefficient and linear change rate between the castable and its internal anchor increases. The linear expansion coefficient of the anchor is 3 times that of the casting. Therefore, during the heating process of the furnace, the heating expansion of the anchor must be considered.
According to the calculation formula of the linear expansion coefficient of the anchor, the radial expansion of a 15 mm anchor at 1 000 ℃ is 0. 28 mm. The castable has an expansion amount, and the linear expansion coefficient of the castable is 6. 36 × 10 – 6 / ℃, which is smaller. The width of the castable is larger than the radial dimension of the anchor. In actual use, the castable has a shrinkage problem due to water. Therefore, a treatment thickness, such as an expansion and contraction gap of 0.2 to 0.37 mm, should be left for the surface treatment of the anchor in the castable. At the same time, the temperature of the castable in the vertical direction of the kiln barrel is different, and the radial expansion of the anchor is also different. Therefore, the expansion and contraction gap in the direction close to the kiln barrel at a low temperature should be smaller.
As the temperature increases, the linear expansion coefficient and linear change rate of the refractory castable and its internal anchor are greatly different. Therefore, during the heating process of the kiln, the heating expansion of the anchor must be considered. According to the calculation formula of the linear expansion coefficient of the anchor, the radial expansion of a 9mm anchor at 1000 ℃ is 0.17 mm. According to a similar method, the expansion coefficient and linear change rate of anchors, refractory materials, and kiln steel structures of different parts and materials can be calculated to analyze their expansion performance. If the temperature of the kiln barrel increases, the radial expansion of each 10 mm thickness at 400 ℃ increases by more than 10 times compared with 300 ℃. Therefore, an appropriate expansion and contraction gap should be left on the surface treatment of the anchor in the castable, and the expansion and contraction gap close to the kiln tube should be smaller. The linear expansion coefficient of the castable at 200 ℃ is higher than that of the precast brick, and the increase is large. The baking speed of the castable and precast brick should be slower to avoid abnormal expansion.
Therefore, even high-quality refractory castable products will not have the effect of long-life furnace lining if they are not properly constructed. When constructing the castable, expansion joints should be reasonably reserved, and the construction should be reasonable and correct.
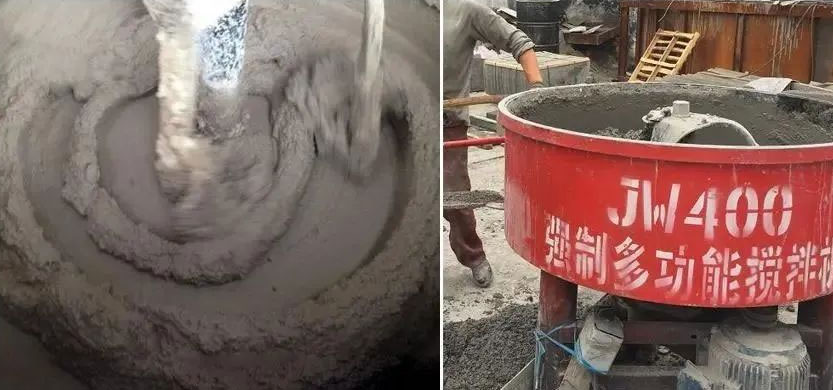
How to Mix Refractory Castables?
Refractory castables are supplied in the form of mixed materials in small bags in ton bags, so the operation of construction pouring on site is also very important.
When mixing refractory castables, first pour the small bags of bulk materials in the ton bags and the small bags of binders in the bags into the mixer, and dry mix them for 3-5 minutes to make them evenly mixed. According to the specified amount of water, accurately weigh the drinking water required for each mixing, pour it into the mixed dry materials, and stir it thoroughly for no less than 1-3 minutes to make it have appropriate fluidity. The castable can be poured after it becomes a paste. Usually, vibration-molded refractory castables, like refractory ramming materials, require support templates for lining construction. The construction body is cured, hardened, demoulded and dried on site before it is put into use.
The performance of the castable depends on its fluidity, and water is the key binder in the castable. Water acts as a medium during the pouring process of castables. In order to obtain a good refractory castable lining, the amount of water added must be strictly controlled. Because high water consumption will cause the aggregate to separate and deposit from the powder, so that a large amount of water will escape during the drying process of the refractory castable, resulting in more pores, that is, pores, which will cause the castable structure to be loose and the performance to decrease.
Water can fill the gaps between particles. If the amount of water added is appropriate, the bulk density of the powder will be large. It can also increase the fluidity of the castable. This requires a reasonable process ratio of the castable. Coarse particles will reduce the fluidity of the refractory castable slurry, but can improve the strength of the castable and reduce post-burning shrinkage. Coarse particles form channels for water vapor to escape during the drying process. Avoid damage to the refractory castable structure when water vapor escapes, but the appropriate ratio is best.
It is a very important process to mix the castable with water to make a slurry. The stirring time cannot be too short. Too short will not produce force during the mixing process. Even mixing can improve the performance of the castable. But it cannot be too long, otherwise it will cause the loss of traction and poor fatigue resistance during use.
The fine powder and micro powder in the refractory castable have agglomeration properties. In the early stage of adding water, the particles will be covered by the liquid film of the adsorption layer, which plays a role in connecting and reducing tiny pores. The number of particles wrapped by water makes the castable wrap as a whole. The effect is better.
Therefore, when constructing refractory castables, reasonable water addition and stirring are the first steps.
Leave Your Requirements on RS Kiln Refractory Bricks And Castable Materials! We Will Reply You In 12 Hours!: