Low-porosity clay bricks can be made into various types of bricks suitable for the production needs of the kiln according to the different kilns it is used in. Rongsheng refractory brick manufacturers also have a lot of experience in refractory bricks for glass kilns, including AZS bricks, zirconium bricks, and clay bricks.
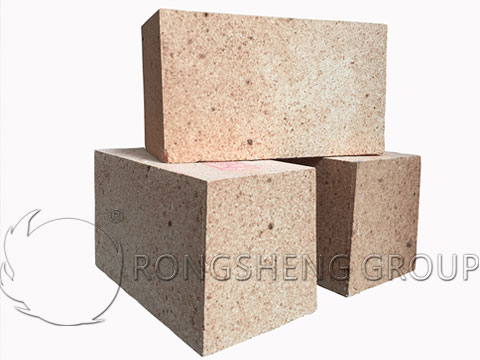
Low porosity clay bricks for glass kiln
The porosity of clay bricks is generally 24-26%, while low-porosity clay bricks are mostly used between 12-16%, and some porosity is less than 10%. The low porosity of low porosity clay bricks mainly depends on the coke stone to adjust the porosity. The performance of low-porosity clay bricks after adding burnt stones is improved, and the compactness, strength and erosion resistance are improved. The sintering temperature of low-porosity clay bricks is high, the raw material matrix changes greatly, and the erosion resistance, thermal shock resistance, and strength are further improved. The application of low-porosity clay bricks is widely used in metallurgical building materials, petrochemicals, ceramic glass, hot blast stoves, and glass furnace regenerators.
Refractory bricks for the lower layer of the lattice body and other parts of the glass furnace
The temperature of the lower layer of the lattice body of the glass furnace is below 800°C, and the chemical erosion is weak, but the total weight of the lattice body of a regenerator is at least 40-50t, and the unit load of the lower layer of the lattice body is as high as 8-10t/m2. Therefore, it is advisable to use high-quality low-porosity clay bricks with strong creep resistance and good thermal shock resistance. In order to prevent the contact reaction between alkaline bricks and clay bricks, high alumina bricks can be used as a transition layer between the middle and lower layers of the lattice body.
Other parts of the regenerator of the glass furnace include the roof, side walls, bars, etc. The erosion of refractory materials in these parts is relatively weak. Generally, the top of the regenerator is made of high-quality silica bricks. The side wall is divided into three parts, and high-quality silica bricks are used for the regenerator wall in the upper space of the lattice body. The target wall can also be directly combined with magnesia-chrome bricks, from the part above the furnace bar to the height of the top surface of the lattice body. A better solution is to use the same material as the lattice body in the same height section, which can prolong the service life of the wall. Another option is to use alkaline bricks one level lower than the corresponding lattice material in the upper section or directly combine magnesia-chrome bricks. The middle section uses directly bonded magnesia-chrome bricks, and the lower section uses clay bricks with low porosity. The first-grade clay bricks can be used below the grate. The furnace grate is generally made of clay bricks with low porosity, and it can also be made of cast AZS material with clay guard bars.
Properties and Requirements of Clay Bricks for Glass Furnaces
Clay products are acidic refractory products, and their acidity increases with the increase of SiO2 content. It has a certain corrosion resistance to acidity, but poor resistance to alkaline corrosion. There are different varieties of clay bricks, such as low porosity clay bricks, porosity clay bricks, low creep, low porosity, low iron clay bricks, and so on. Therefore, clay products are suitable for refractory materials for acid kilns. Large clay bricks for glass kilns are clay refractory bricks with a unit weight of not less than 50kg for masonry glass kilns.
The use conditions of clay bricks are different due to different molding methods and aggregates and binders of clay bricks. According to these characteristics, different types of clay bricks can be used in different parts of the pool furnace due to different erosion conditions. The grate bars and checker bricks in the lower part of the regenerator are less eroded by batch dust and volatile matter, the temperature is lower, and the load is heavy, so this kind of brick requires high mechanical strength. Therefore, the binder in the brick can contain an appropriate amount of SiO2 and Fe2O3. However, clay bricks used in high-temperature parts mainly require high refractoriness and fewer impurities in the combination.
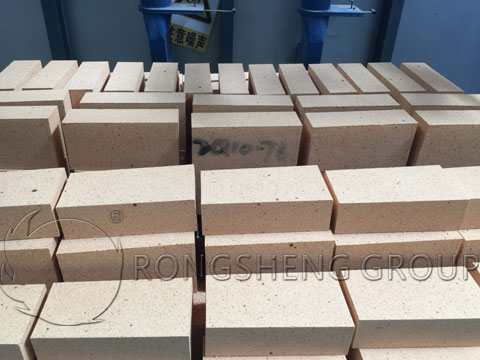
Application of glass kiln low porosity clay brick
Low-porosity clay bricks are mainly used in the regenerator of glass kilns. It can also be applied to blast furnaces and hot blast stoves in the steel industry. Cement kilns in the building materials industry, chemical kilns in the chemical industry, and other kilns are used as the lining of kilns.
Advantages of low porosity clay bricks
The key to making low-porosity clay bricks is to choose raw materials with high density and low water absorption, and through reasonable gradation. When firing clay bricks, the temperature is generally controlled at 1350°C to 1380°C. Appropriately increasing the firing temperature of low-porosity clay bricks (1420°C), the shrinkage of clay bricks increases slightly, thereby slightly increasing the density of refractory bricks and reducing low porosity.
Due to the addition of additives, a large number of micropores are formed inside the clay brick during the firing process. Before the clay brick breaks as a whole, the internal micropores can prevent and inhibit the cracking of the clay brick. As clay bricks for iron ladles are used under high-temperature thermal shock conditions, cracks on the surface will not cause fractures during use. The serious one is thermal spalling caused by internal thermal stress. When the porosity is appropriately reduced and a large number of micropores are generated, the length of cracks inside the clay bricks becomes shorter and the number increases under thermal shock, and the degree of the interlacing of cracks to form a network is enhanced. Therefore, the fracture energy required for clay brick fracture increases, which can effectively improve the thermal shock stability of clay bricks, improve the peeling resistance of clay refractory bricks, and greatly increase the service life of kilns.
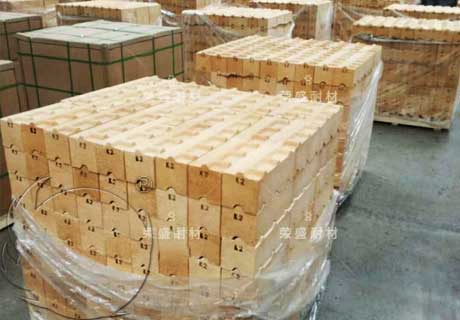
Rongsheng Refractory Brick Manufacturer
Rongsheng refractory brick manufacturer, high-quality low-porosity clay bricks, provides high-quality refractory brick products for carbon roasting furnaces and glass kiln regenerators. Rongsheng is a high-quality refractory brick manufacturer, providing high-quality refractory brick products for various industrial kilns. The price of low-porosity clay bricks for a glass kiln, how much is a ton of low-porosity clay bricks for a glass kiln? As a manufacturer of refractory bricks, we will provide you with a comprehensive quotation based on raw materials and other factors. Due to various uncertain factors, the price of low-porosity clay bricks may fluctuate, please contact us for the specific price of low-porosity clay bricks. According to your production needs, we will provide you with the most suitable refractory brick products for your production needs.
Leave Your Requirements on RS Kiln Refractory Bricks And Castable Materials! We Will Reply You In 12 Hours!: