Magnesia-alumina brick refers to an alkaline refractory material that is made of magnesium oxide and industrial alumina or alumina as raw materials, crushed, shaped, and fired at about 1600°. Magnesia-alumina bricks have a fire resistance limit of more than 2000°C, good rapid cooling and heat resistance, and can resist the erosion of alkaline slag. Used for laying the roof of alkaline open-hearth furnaces and electric furnaces for steelmaking.
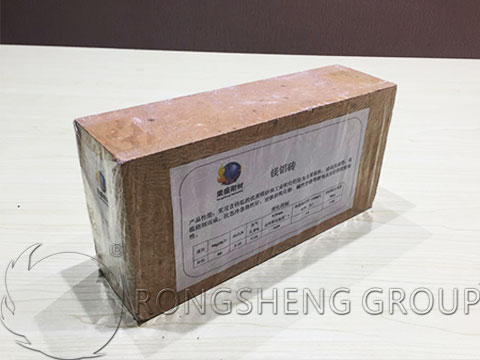
Performance Characteristics of Magnesia-Alumina Bricks
There are three types of magnesia-alumina bricks, all of which are alkaline refractory materials. Magnesia-alumina bricks include ordinary magnesia-alumina bricks, magnesia-alumina spinel bricks, and modified magnesia-alumina spinel bricks. During the firing process of magnesia-alumina bricks, MgO and Al2O3 react at high temperatures to form the high-temperature mineral phase of magnesia-alumina spinel. Magnesia-aluminum spinel has a small thermal expansion coefficient and good uniformity, which can reduce thermal stress caused by temperature changes.
- Ordinary magnesia-alumina bricks. Magnesia-alumina brick is a spinel-type alkaline refractory material containing about 85% MgO and 5% ~ 10% Al2O3. The crystal phase composition of magnesia-alumina bricks is mainly periclase and magnesium-alumina spinel as the matrix. After the spinel aggregate crystallizes, it forms a crystal network, making the brick structure dense. Since no coarse aggregate is used in manufacturing, the overall brick structure is uniform and the pores are loose.
- Magnesia-alumina spinel brick is a kind of magnesia brick with magnesium-alumina as the main mineral resource. It is made by adding alumina to the ingredients to improve the thermal stability of the magnesia brick. Magnesia-alumina spinel bricks have the advantage of good thermal stability and will chemically react with clinker during use. Then a thin protective layer of calcium aluminate is formed on the outside of the brick, and its anti-falling performance is better than that of directly bonded magnesia-chromium bricks.
- Modified magnesia-alumina spinel bricks. Magnesia-alumina spinel bricks have been successfully used in the transition zone of cement inversion kilns. However, they are easy to become brittle and fall off in the firing zone. The kiln skin is not easy to hang materials. The cement clinker has poor resistance to alkali vapor and liquid phase penetration, and the kiln body has poor resistance to penetration. Poor mechanical stress capability caused by deformation limits its application in fired zones. To this end, modified magnesia-alumina spinel bricks suitable for cement reverse kiln sintering zones were developed.
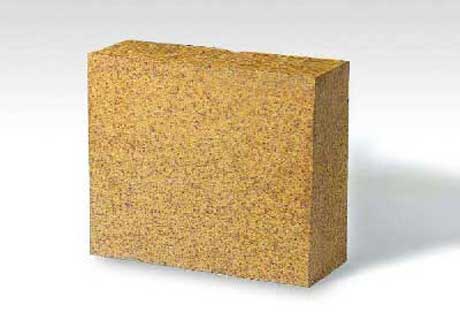
Application of Magnesia-Alumina Bricks
Magnesia-alumina bricks are widely used in non-ferrous metallurgical furnaces, magnesia-alumina spinel bricks are widely used in cement conversion, and modified magnesia-alumina spinel bricks are widely used in cement reverse kiln sintering zones. The thermal shock resistance of magnesia-alumina bricks is better than that of magnesia bricks, and the softening temperature under load is higher than 1580 degrees. The softening temperature of high-purity magnesia-alumina bricks under load can reach 1600 ~ 1750 degrees. In addition to the impurity content in magnesia-alumina bricks, with the addition of A1203, the load softening start temperature generally increases, and there is a higher value when the A1203 content is 3% to 10%. When the A1203 content exceeds 10%, it begins to decrease. When the temperature is lower than 1000 degrees, the elastic modulus of magnesia-alumina bricks increases with the increase in temperature, but when the temperature exceeds 1000 degrees, the elastic modulus decreases significantly.
Comparison between Magnesia-Alumina Bricks and Magnesia Bricks
RS Kiln Refractory Manufacturer provides a wide range of high-quality magnesia alumina brick products. Magnesia-alumina bricks have a wide range of types and applications. RS Kiln Refractory manufacturers customize magnesia-alumina brick refractory lining solutions based on the production characteristics of high-temperature industrial furnaces. Compared with magnesia bricks, magnesia-alumina bricks also have the following characteristics.
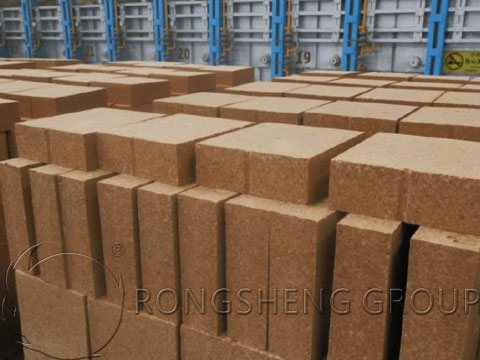
(1) Magnesia-alumina bricks have good thermal shock resistance and can withstand water cooling 20 to 25 times, or even higher. This is its most prominent advantage, much better than ordinary magnesia bricks.
Research suggests that magnesia-alumina bricks have good thermal shock resistance because both magnesia-alumina spinel and periclase belong to the equiaxed crystal system. The linear expansion coefficient of magnesia-aluminum spinel is small, and the thermal expansion along each crystal axis direction is the same. Therefore, the expansion and contraction are relatively uniform when the temperature fluctuates, and the thermal stress generated is small.
(2) The main properties of magnesia-alumina bricks are also slightly stronger than magnesia bricks. Because the melting point of magnesia-alumina spinel itself is higher, the load softening temperature of magnesia-alumina bricks is improved than that of magnesia bricks, reaching 1620℃~1690℃.
(3) The ability of magnesia-aluminum spinel to protect periclase particles from slag erosion is stronger than that of forsterite. Therefore, the ability of magnesia-alumina bricks to resist alkaline slag and iron oxide slag is stronger than that of magnesia bricks.
Magnesia-alumina bricks have many of the above excellent properties, so they are widely used as masonry materials for the roofs of high-temperature smelting furnaces such as steel-making open-hearth furnaces and copper-making reverberatory furnaces, and have the effect of extending the life of the furnace. A large open hearth furnace can hold about 300 furnaces, and a small and medium-sized open hearth can hold more than 1,000 furnaces.
Leave Your Requirements on RS Kiln Refractory Bricks And Castable Materials! We Will Reply You In 12 Hours!: