The dry quenching coke oven system consists of a quenching chamber, a primary dust collector, a high-temperature expansion joint, a waste heat boiler and a secondary dust collector. The dry quenching chamber adopts a circular design, which is divided into an upper cone, a pre-storage section, an inclined air duct, a cooling section and a lower cone from top to bottom. Most of the refractory materials of the dry quenching coke oven system lining are made of refractory bricks, and only a small number of parts use amorphous refractory materials. In recent years, due to various reasons, the refractory bricks in the inclined air duct have broken after 1 to 2 years of production, and normal production cannot be carried out. The refractory bricks in the cooling section have been subjected to the friction of cold coke for a long time, and have been seriously worn after more than one year of production. The castables at the high-temperature expansion joint and the boiler inlet are often easy to fall off during the production process.
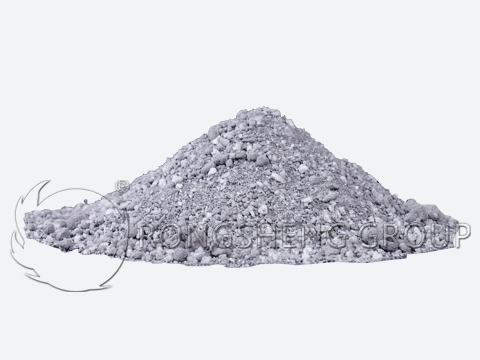
Maintenance of the Cooling Section of the CDQ Coke Oven
Due to the long-term friction of cold coke, the wear resistance of mullite refractory bricks in the cooling section cannot meet the production needs, and the refractory bricks are seriously worn after more than one year of production.
The CDQ cooling section uses plastic for overall ramming and has achieved certain results. Plastic uses mullite silicon carbide as the matrix material and phosphoric acid and aluminum phosphate as the binder. Combined with micro-powder technology, it is processed through processes such as trapped materials, mixing, extrusion, cutting, packaging, and storage. It is also called wear-resistant plastic. In order to ensure the effective combination between plastic and the original worn refractory brick masonry. It is necessary to apply adhesive on the surface of the original masonry to connect the new and old materials and enhance the integrity between the new and old materials. The adhesive is composed of high-grade fine powder of plastic isomorphous quality, binder and admixture. At the same time, composite admixtures are added to adjust the bonding time and improve the flexural bonding strength.
The current effective maintenance method for the cooling section is to pour a layer of 80-100 mm thick castable on the surface of the damaged masonry. To withstand the wear of coke, thermal stress spalling and gas impact. To protect the stability of the structure above the ramp, this wear-resistant castable is used. The application effect is good and it can generally be used for more than two years.
In addition, wear-resistant castables are used to make prefabricated bricks as the working layer of the cooling section. The original worn refractory bricks are removed and rebuilt with prefabricated bricks. This method can generally be used for more than 4 years.
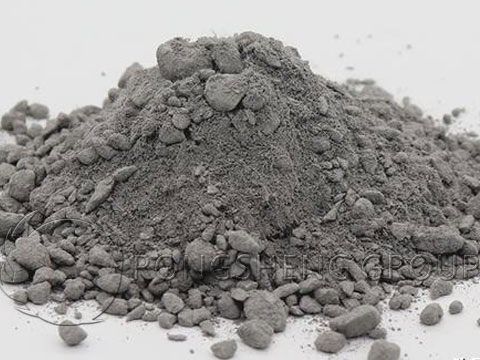
Maintenance of the Inclined Air Duct of the Dry Coke Quenching Oven
The refractory bricks of the supporting part of the inclined air duct are cantilevered layer by layer to support the load of the upper masonry. The temperature fluctuates frequently, and the circulating gas carries coke dust to scour this part violently. Therefore, the inclined air duct area is built with mullite-silicon carbide bricks with high thermal shock resistance, wear resistance and flexural strength. From the current use situation, the effect is not ideal. Some supporting bricks in the inclined air duct area of dry coke quenching break in less than a year.
For the maintenance of the supporting bricks of the inclined air duct, one method is to use the original mullite-silicon carbide bricks to rebuild. Another method is to use castables for casting. The third method is to use wear-resistant castable precast refractory blocks for rebuilding.
The casting method of castables uses anchors and reinforcements. After the residual bricks are removed, high-strength and wear-resistant aluminum silicon carbide steel fiber castables are used for repair. In order to solve the bonding between bricks and castables, holes are drilled on the surface of the original bricks and fixed with expansion bolts. A certain length of “Y”-shaped stainless steel anchor is welded outside the expansion bolt. The length of the anchor should be 50mm away from the original working surface. The disadvantage of this method is that the castable falls as a whole, which damages the original refractory bricks and is inconvenient to repair again in the future.
Castable prefabricated blocks are used to improve the strength, wear resistance, and thermal shock resistance of the inclined air duct support. High-strength wear-resistant castable precast refractory blocks are used instead of bricks, and castable prefabricated blocks are used to replace damaged refractory bricks. This method has a good effect and can generally be used for more than two years.
Maintenance of High-Temperature Expansion Joints and Boiler Inlet of Dry Coke Oven
High-temperature expansion joints and boiler inlet are the parts of the dry coke quenching system that are constructed with castables. However, the castables at the high-temperature expansion joints and boiler inlet are often easy to fall off due to the strong erosion of material particles and corrosive gases at high temperatures, causing deformation and burning accidents of the external steel structure. As a result, the system has to be overhauled in advance. The castables at the high-temperature expansion joints and boiler inlet generally fall off and are damaged within less than a year of use in production.
In order to improve the physical and chemical properties of the heavy castables on the working surface and extend the service life of the refractory materials, mullite-silicon carbide refractory castables that are more suitable for the working environment of the dry coke quenching system can be used. Another more effective way is to use refractory brick masonry for the high-temperature expansion joints and boiler inlets. Remove the heavy castables, lightweight castables and anchors at the high-temperature expansion joints and boiler inlets, and use mullite bricks and lightweight insulation bricks for masonry.
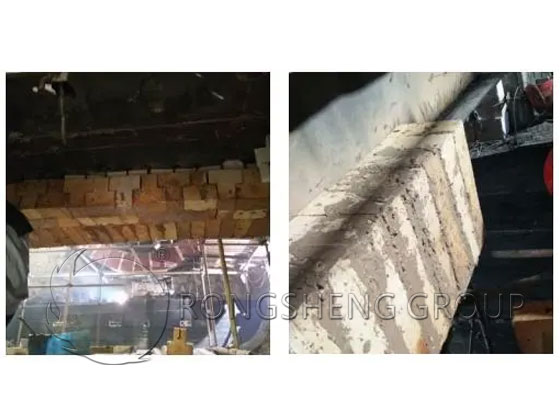
Precautions for CDQ Coke Oven Restart
Before CDQ coke oven restarts, the focus is on the maintenance and drying of castables. If the CDQ coke oven cooling section and inclined air duct are used for castable construction, warm air drying should be carried out first to remove a large amount of moisture in the castable. It is not recommended to directly use red coke oven to prevent the castable from bursting or cracking due to excessive temperature. After warm air drying for about 3 days, red coke can be added and the red coke oven can be used.
Application Advantages of Unshaped Refractory Castables
With the advancement of science and technology and the development of production, the application and development of amorphous refractory materials are also advancing with the times. The rapid development of monolithic refractory materials has increased the production proportion to 60~70% now, and the production proportion of monomorphic refractories in my country has also reached about 40%.
Monolithic refractory materials are refractory materials that can be used directly after the loose mixture is delivered and shaped and baked without pre-firing. According to the construction and production methods, they are classified into castables, ramming materials, plastics, spray coatings, refractory mud, etc. Refractory castables are the most prolific and fastest growing material among monolithic refractory materials, accounting for approximately 55% of all monomorphic refractory materials.
The main advantages of amorphous refractory materials include: simple process, energy saving, and low cost. It can carry out mechanized operations and has high construction efficiency. It can be shaped in any shape and made into an integral lining body with good thermal shock stability. High strength, strong peeling resistance, enhanced service life. It can be partially repaired, online or offline, to improve the operation rate.
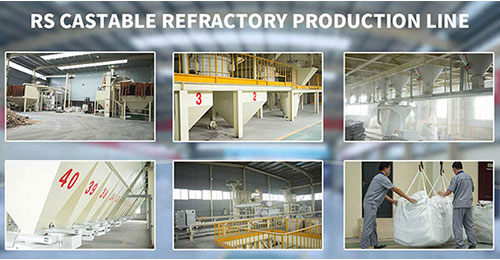
Buy high-quality refractory castable products for high-temperature industrial furnaces, RS Kiln Refractory Company can provide high-quality monolithic refractory services. Customized formulation of unshaped refractory castables and solutions for refractory lining. Wear-resistant refractory castables, wear-resistant plastics, etc. Refractory Precast Shapes, etc. Contact us to get free samples and quotes.
Leave Your Requirements on RS Kiln Refractory Bricks And Castable Materials! We Will Reply You In 12 Hours!: