Blast furnace tap trough castable is a common lining material for tap trough lining. The tap trench is a channel for molten iron to flow through. During use, it is subject to erosion by molten iron, chemical erosion of iron slag, oxidation of air, and thermal shock stress caused by temperature fluctuations. Therefore, the selected refractory castable ratio must meet the above characteristics. Nowadays, high-aluminum silicon carbide carbonaceous castables or corundum-based silicon carbide carbonaceous castables are mostly used, referred to as ASC castables.
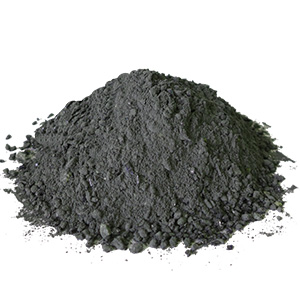
ASC castables for tap trenches are generally low-cement or ultra-low-cement castables. It is mainly composed of Al2O3 aggregate, SiC, carbon, cement, and various additives. High-purity raw materials are used, the composition and particle size of the materials are adjusted, and it has fast drying and anti-explosion properties. Adding a small amount of metal Al powder, adding a small amount of organic foaming agent, and adding a small amount of organic fiber has better oxidation resistance. Add a small amount of Si powder, add ferrosilicon nitride, and add high-efficiency de-flocculant. Add a small amount of polyphosphate. The functions of various materials are as follows.
Raw Material Configuration and Performance of ASC Castables for Blast Furnace Tap Trough
Al2O3 aggregates mainly include fused corundum, brown corundum, white corundum, sintered alumina, and high alumina bauxite clinker. When using, it should be selected according to the usage conditions of the material. High-grade materials use fused dense corundum, mid-grade materials use brown corundum, and low-grade materials use sintered corundum.
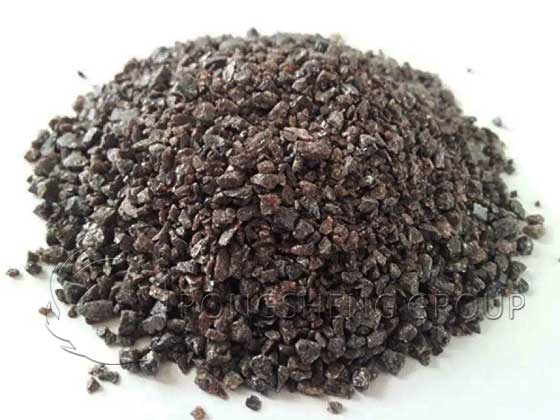
The role of SiC raw materials. 1. Can effectively prevent carbon oxidation. 2. SiC has a low expansion coefficient, which can prevent cracking of ASC castables during heating and cooling. 3. SiC has high thermal conductivity, which can improve the thermal shock stability of ASC castables. 4. SiO2, CO, and CO2 generated after SiC oxidation can effectively inhibit the oxidation of materials. 5. SiC can effectively improve the impact resistance of the material.
The role of carbonaceous raw materials. 1. It can prevent the internal penetration of slag phase materials and improve the corrosion resistance of the materials. 2. It can improve the thermal conductivity of the material, improve the thermal shock stability of the material, and reduce the structural peeling and cracking of the material. 3. Carbon can be added using graphite, carbon black, pitch coke, and other raw materials.
The role of pure high alumina cement. 1. High alumina cement is added to maintain the low and medium temperature strength of the material. 2. When adding high alumina cement, a small amount of CaO will be brought in, which is not conducive to the corrosion resistance of the material. 3. As the amount of high alumina cement added increases, the water demand of the material increases, the pores of the castable increase, and the corrosion resistance also decreases. Therefore, the current development trend of castables is low cement and ultra-low cement ASC castables.
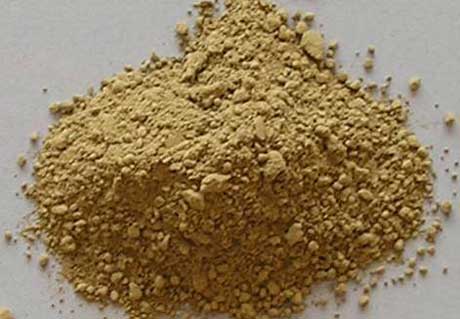
The role of silica powder. Adding silicon powder can generate SiC with the carbon in the material. On the one hand, it can improve the high-temperature strength of the castable, and on the other hand, it can improve the oxidation resistance and slag resistance of the castable.
The role of metal aluminum powder. 1. Because metal aluminum powder can react with water in the castable to generate H2 for elimination. Leaving small vents can remove some free water and prevent popping during baking. 2. The heat generated during the hydration reaction can accelerate the dehydration speed, accelerate the condensation and hardening of the castable, and improve the strength of the castable. 3. The amount of metal aluminum powder added should not be too much. Otherwise, the structure of the material will be loose, the strength will be reduced, and the erosion resistance will become worse.
The role of organic fibers. Prevent the castable from exploding during baking. It is conducive to the elimination of water vapor, improves baking quality, and shortens baking time.
The role of sodium polyphosphate. 1. It has the effect of dispersing and reducing water. It can increase the bulk density of materials, reduce porosity, increase strength, and improve construction performance. 2. The sodium polyphosphates used are mainly sodium tripolyphosphate and sodium hexametaphosphate.
High-quality ASC castables made of the above refractory raw materials have the following advantages. 1. It has excellent high-temperature wear resistance and strong resistance to erosion by molten iron and slag. 2. It has good chemical corrosion resistance permeability of slag, and strong oxidation resistance. 3. It has good thermal shock resistance and burst resistance. 4. The volume change after re-burning is small and it has a dense and uniform structure. 5. Strong resistance to various oxidants. 6. Easy to construct and disassemble, non-stick slag, easy to clean iron slag.
Rongsheng Kiln Refractory Factory
Rongsheng Kiln Refractory Factory can provide various refractory lining materials for steelmaking industrial furnaces, with reliable product quality and guaranteed customer service. Our professional technical team can customize refractory lining solutions according to actual industrial furnace conditions. Contact us for a free quote.
Leave Your Requirements on RS Kiln Refractory Bricks And Castable Materials! We Will Reply You In 12 Hours!: