Aluminum electrolytic cell is the main thermal equipment for aluminum electrolysis production. Electrolytic aluminum is the process of converting aluminum in alumina into metallic aluminum. The main principle of its transformation is to use cryolite and aluminum oxide melt as the electrolyte, and carbon materials as the two poles. Direct current is introduced into the electrolyte and aluminum liquid layers through the anode, and then derived from the cathode.
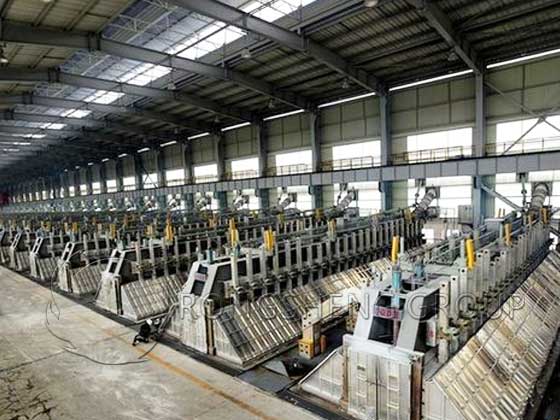
During the construction process of aluminum electrolytic cells, refractory materials and carbon materials are mainly used as masonry materials. Its varieties are as follows:
Refractory Materials for Aluminum Electrolytic Cells
- Calcium silicate board.
Calcium silicate board is reinforced with loose short fibers such as inorganic mineral fibers or cellulose fibers. A board made of siliceous-calcium material as the main cementing material, which is pulped, shaped, and accelerated in high-temperature and high-pressure saturated steam to form calcium silicate gel. Calcium silicate boards can be divided into two types according to their use, namely calcium silicate boards for building materials and calcium silicate boards for high-temperature kilns. Calcium silicate boards used in high-temperature kilns require high-temperature resistance ≥1050°C. The calcium silicate board complies with national standard GB/T10699.
- Clay insulating refractory bricks.
Clay insulating refractory bricks refer to insulating refractory products with an Al2O3 content of 30% to 48% made of refractory clay as the main raw material. Using refractory clay, floating beads and refractory clay clinker as raw materials, adding binder and sawdust, through batching, mixing, shaping, drying, and firing, products with a bulk density of 0.3~1.5g/cm3 can be produced. Its production accounts for more than half of the total output of insulating refractory bricks. Clay insulating refractory bricks comply with national standard GR/T3994.
- Clay refractory bricks.
Clay refractory bricks are clay bricks produced from refractory clay and used to build the lining of blast furnaces. Its Al2O3 content is ≥45%. Clay bricks are weakly acidic refractory products that can resist the erosion of acidic slag and acidic gases, but have slightly less resistance to alkaline substances. Clay bricks have good thermal properties and are resistant to rapid cooling and heating. Clay refractory bricks comply with standard YB/T5106-1993.
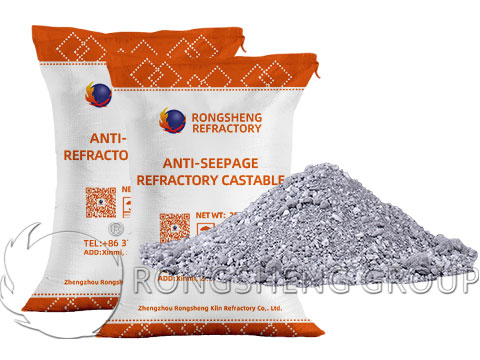
- Dry anti-seepage material
Dry anti-seepage material is a functional material specially used for building aluminum electrolytic tank furnaces. It has a significant effect on improving the technical and economic indicators of electrolytic cells and extending the service life of electrolytic cells.
Carbon Materials for Aluminum Electrolytic Cells
- The electrolytic cell uses ordinary cathode carbon blocks.
Cathode carbon blocks refer to carbon blocks made from high-quality anthracite, coke, graphite, etc. Used as a cathode in aluminum electrolytic cells. It is built at the bottom of the electrolytic cell and is also called the bottom carbon block. Cathode carbon block is an important part of the aluminum electrolytic cell, which is beneficial to energy saving in aluminum electrolytic production and improving the life of the cell. Common cathode carbon blocks for electrolytic cells. Comply with industry-standard YS/T286-1999. The appearance should comply with the following requirements:
-
- (1) The surface of the carbon block is smooth, and the cross-sectional structure is free of holes, delaminations, and inclusions.
- (2) The bonding filler on the surface of the carbon block must be cleaned.
- (3) The carbon blocks are strictly prohibited from getting wet and contaminated with oil.
- Semi-graphite cathode carbon block for electrolytic cells.
Semi-graphite cathode carbon block complies with national standard GB8744-1988. The appearance should comply with the following regulations: the product surface should be smooth, and the cross-sectional structure is not allowed to have holes, delaminations and inclusions.
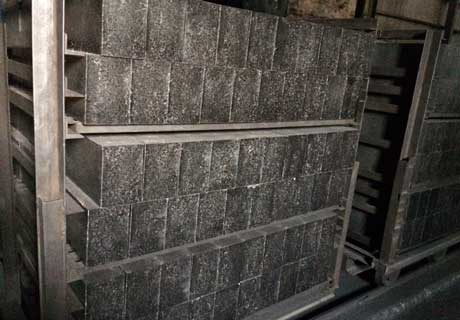
- Charcoal paste
The charcoal paste includes hot charcoal paste and cold charcoal paste.
(1) Hot ramming rough seam paste, comply with the metallurgical industry-standard YS65-1993. There are two recipes for caulking paste. The rough seaming paste used to connect the steel rod and the cathode carbon block uses Formula 1, and the rough seaming paste used to strengthen the seams between the carbon blocks uses Formula 2.
(2) Cold pounded charcoal ingredients:
- LTC-1 is suitable for the joint between the electrolytic cell pad and filled carbon block or electrolytic cell lining.
- LTC-2 is suitable for the joint between the cathode carbon block and the cathode steel rod in an electrolytic cell.
In addition to the above-mentioned refractory materials and carbon materials, materials such as water glass asbestos putty, and silicon nitride combined with silicon carbide are also used in aluminum electrolytic cells. Rongsheng kiln refractory material manufacturer is a powerful manufacturer of refractory materials production and sales. We have mature experience in aluminum electrolytic cell projects. Contact us for a free refractory solution and quote.
Leave Your Requirements on RS Kiln Refractory Bricks And Castable Materials! We Will Reply You In 12 Hours!: