Electric furnace is the main equipment for yellow phosphorus production. Qualified phosphate rock, silica and coke are made into a mixed charge in a certain proportion and added to the electric furnace to carry out the reduction reaction at 1300~1500°C. The generated phosphorus-containing furnace gas is dedusted, condensed and refined to obtain the finished product yellow phosphorus, and the by-products slag and iron phosphorus are regularly discharged from the bottom of the furnace. Therefore, there are strict requirements for the insulation materials, refractory materials and furnace lining refractory brick structure in the furnace lining.
Characteristics of Refractory Materials for Phosphorus-Making Electric Furnaces
The furnace body of the phosphorus-making electric furnace is composed of a steel shell and refractory materials. The charge undergoes a chemical reaction in the furnace, and the generated molten slag and ferrophosphorus accumulate in the lower part of the furnace, causing slag corrosion. Therefore, the requirements for this part of the furnace bottom and furnace lining refractory materials are relatively high: high load softening temperature, good resistance to slag erosion, small expansion coefficient, good thermal stability, and high compressive strength. Generally, the refractory materials for yellow phosphorus electric furnace lining are composed of high alumina bricks, carbon bricks, and cold rammed paste. The furnace roof is mostly made of steel fiber refractory castables or high-strength refractory castables.
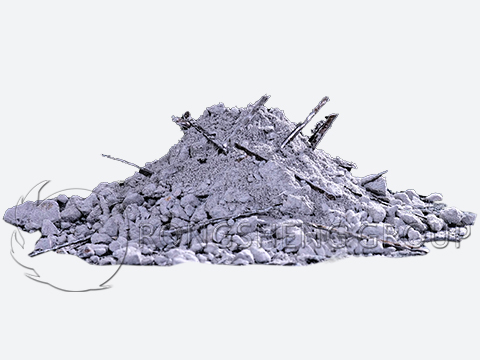
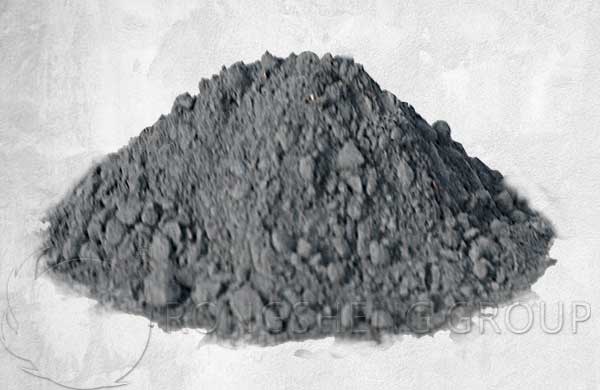
During the normal production process, the furnace lining will be corroded by molten slag, and the degree of corrosion of the furnace lining is related to the maintenance cycle of the electric furnace. Therefore, generally speaking, the degree of corrosion of the furnace lining determines the service life of the phosphorus-making electric furnace, which also determines the overhaul interval of the electric furnace phosphorus-making device. Therefore, when it comes to key issues such as the quality of furnace lining refractory materials, construction and installation, and furnace lining masonry, quality must be strictly controlled. To extend the service life of electric furnaces for phosphorus production and save production costs.
Analysis of Causes of Damage to Yellow Phosphorus Electric Furnace Lining
When the phosphorus-making electric furnace is operating normally, the slag temperature in the lower molten pool is about 1500°C. The high-temperature furnace gas undergoes sufficient heat exchange through the material layer several meters thick from bottom to top, causing its temperature to gradually decrease. When it rises to the upper space of the furnace, the temperature drops to about 220~300℃, and the slag temperature in the center of the furnace molten pool is about 1500℃. Due to the heat dissipation effect of the furnace body, the temperature gradually decreases from the center to the furnace wall and furnace bottom, and is about 1000~1200°C at the place where materials are hung on the furnace wall. The higher the temperature of the slag, furnace wall and furnace bottom, the more corrosive it will be to the furnace lining carbon bricks. The bottom and walls of the furnace are generally cooled by air or circulating water. In daily production, the expected furnace cooling effect must be achieved.
(1) Furnace lining corrosion environment analysis
Phosphate rock, silica and coke are inherently non-corrosive. However, the proportion of silica, coke and phosphate rock in the furnace charge is inappropriate and the coke particle size is too large, causing a chemical reaction in the furnace. It will cause severe corrosion of the furnace lining during the production process. The melting point of slag determines the m(SiO2)/m(CaO) acid-base composition of the CaO-SiO2 system. That is, judging from the acidity index Mk of the slag, when m(SiO2)=51.7% and m(CaO)=48.3%, the melting point of CaSiO3 is the highest, which is 1540°C. At this time, the acidity index of molten calcium silicate is MK = 1.07. Slags with MK less than 1.07 are called basic slags, and those with MK greater than 1.07 are called acidic slags. However, the melting point of slag with an acidity index slightly larger or slightly lower than 1.07 is lower than that of CaSiO3, so slag with an acidity index MK close to 0.8 or 1.2 can be used in production operations. Since acidic slag is highly corrosive to the furnace lining, it should not be used. When operating with alkaline slag, the acidity index of the slag is generally controlled at MK =0.75~0.85. Due to the presence of a small amount of impurities in the slag, its melting point is lowered. Therefore, the molten slag temperature controlled by the low melting point indicator is 1250~1450℃.
(2) Erosion of furnace lining liquid
The molten slag and phosphorus iron are affected by the high temperature at the end of the electrode, constantly churning and scouring the furnace bottom carbon bricks, sometimes forming pits at the bottom of the molten pool in the electrode triangle area in the center of the furnace. If the joints of the furnace bottom carbon bricks are of poor quality, the molten iron phosphorus will penetrate into the joints of the bricks, causing the carbon bricks to float, ablate and melt. Slag will also corrode the furnace wall carbon bricks, make the furnace shell steel plate red, and even burn through the furnace bottom and furnace wall steel plates.
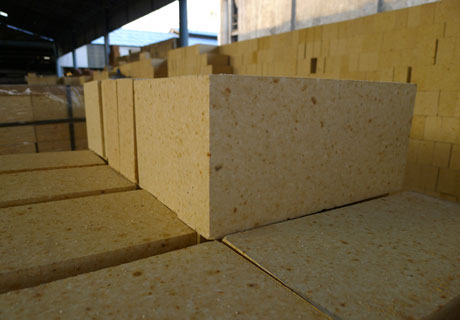

Yellow Phosphorus Electric Furnace Lining Refractory Material Configuration and Masonry
(1) The furnace bottom and furnace walls are constructed with high alumina bricks. According to the Class I masonry standards in the technical requirements for refractory brick masonry construction. The construction of mortar joints <1mm requires dry masonry layer of high alumina bricks with full mud. The finished brick surface should be cleaned before laying the next layer of bricks. When the bricklaying is interrupted or the bricks are removed due to rework and it is necessary to leave a chamfer, it should be left in the form of a stepped chamfer. The height difference between adjacent walls shall not exceed 1.2m. When masonry, a wooden mallet or rubber mallet shall be used for knocking and alignment, and a hammer shall not be used to knock bricks.
(2) The thickness of the horizontal brick joints of carbon bricks is about 20mm. If west joint masonry is used, or self-baked charcoal bricks and cold rammed furnace building techniques are used. When building a furnace, you must pay attention to the product instructions and follow the relevant technical requirements for furnace construction.
(3) When using cold rammed paste or electrode paste as a binder to build the carbon brick furnace lining, it must be heated with a low fire first. The heating and melting temperature of electrode paste is generally controlled at 180~190℃. The height poured into the brick joints each time is 80~100mm, and tamped with a pneumatic pick and hammer so that the compacted height is 40%~50% of the original height. The vertical joints of the upper and lower layers of charcoal bricks on the bottom of the furnace intersect vertically in space. The two layers of carbon bricks inside and outside the furnace wall are built vertically. The brick joints are about 40mm wide and should be staggered with the brick joints of the furnace bottom carbon bricks. Use wooden boards to block the opening to prevent electrode paste from flowing and forming pores to ensure construction quality.
The phosphorus-making electric furnace is the heart equipment of the yellow phosphorus plant and must be operated carefully and standardizedly. Reasonably adjust the addition ratio of raw material ingredients, control the particle size of coke, and strictly control the construction quality of lining refractory materials and the procurement standards of refractory materials. In order to extend the service life of the furnace lining.
RS Kiln Refractory for Sale
RS Kiln Refractory Company is a professional refractory material service provider for high-temperature industries. RS manufacturers provide services such as customization of refractory lining materials, technical services, and complete construction packages of refractory materials. Custom refractory lining solutions. Refractory material configuration and sales for yellow phosphorus furnaces. The main refractory products include various refractory lining bricks, high alumina bricks, carbon bricks, magnesia bricks, etc. Moreover, our environmentally friendly unshaped refractory castable factory specializes in producing a series of high-aluminum castables, non-stick aluminum castables, low-cement castables, steel fiber wear-resistant castables, high-strength castables, silicon carbide castables, etc. Refractory castable products for industrial kilns. Contact us to get a free solution and quote for refractory lining materials.
Leave Your Requirements on RS Kiln Refractory Bricks And Castable Materials! We Will Reply You In 12 Hours!: