Rongsheng Kiln refractory manufacturer produces and sells T-3 magnesium brick 230*114*65 magnesium oxide bricks. The properties of magnesia bricks, magnesia silica bricks, magnesia alumina bricks, magnesia calcium bricks, and magnesia carbon bricks are greatly affected by the ratio of CaO/SiO2 and impurities. The load softening point and thermal shock resistance of high-purity magnesia bricks are better than ordinary magnesia bricks. High-purity magnesia bricks have high refractoriness and good resistance to alkaline slag and iron slag and are an important high-grade refractory material. Magnesia refractory products are mostly produced by sintering, and the firing temperature is generally between 1500 and 1800 °C. In addition, unburned bricks and unshaped refractory materials can also be made by adding chemical binders. Mainly used in open hearth furnaces, electric furnaces, oxidation converters, non-ferrous metal smelting furnaces, cement kilns, and calcining kilns for basic refractory materials, etc.
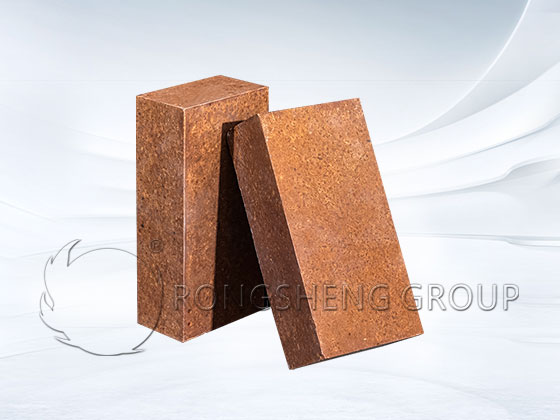
Specifications of T-3 refractory bricks
The well-known refractory bricks are referred to as refractory bricks, which are refractory materials fired from refractory clay or other refractory raw materials. The more common refractory bricks are light yellow or brownish and can withstand high temperatures of 1580°C~1770°C. It is mainly used for building smelting furnaces, high-temperature building materials, and structural materials for building kilns and various thermal equipment, and can withstand various physical and chemical changes and mechanical effects at high temperatures.
There are many types of refractory bricks, and their shapes and sizes are quite complicated, but they all have a unified specified brick number. Through the brick number, you can know the use, shape, size, etc. of the refractory brick. For example, bricks with the prefix T are common brick types for general industrial furnaces. From T-1 to T-105, there are more than 20 shapes, 105 brick numbers, and specifications. For example, T-3 is a commonly used standard brick type, and the size of the refractory brick represented by T-3 is 230*114*65mm. Rongsheng kiln refractory manufacturers can provide T-3 magnesium brick 230*114*65, and other refractory brick products of various types and sizes. Brick type and size can also be customized according to the actual working conditions of the customer’s kiln.
Rongsheng Magnesium Refractory Products
The magnesia refractory products of Rongsheng kiln refractory manufacturers include magnesia bricks, magnesia silica bricks, magnesia alumina bricks, and magnesia chrome bricks.
- (1) Standard type. It is stipulated that 230m×114m×65mm is the standard refractory brick.
- (2) Common type. Those with one of the following classification characteristics are named ordinary products. ①The weight is 4-10kg. ②The thickness size is 55-75mm. ③No more than 4 measuring scales. ④ The size-to-size ratio is not greater than 4. ⑤Without concave corners, grooves, tongues, holes, holes, or arcs.
- (3) Irregular type. Those with one of the following typing characteristics are named irregular-shaped products. ①The weight is 3.5~18kg. ②The thickness size is 45~95mm. ③ The size-to-size ratio is not greater than 6. ④The total number of concave corners and arcs shall not exceed 2. ⑤1 acute angle greater than 50°~75°. ⑥No more than 2 holes or holes.
- (4) special type. Those with one of the following classification characteristics are named special shape products. ①The weight is 3~35kg. ②Thickness size is 35~135mm. ③ The size-to-size ratio is not greater than 8. ④The total number of concave corners and arcs shall not exceed 4. ⑤ The total number of grooves and tongues is not more than 4. ⑥One acute angle of 30°-50°. ⑦ No more than 3 holes or holes.
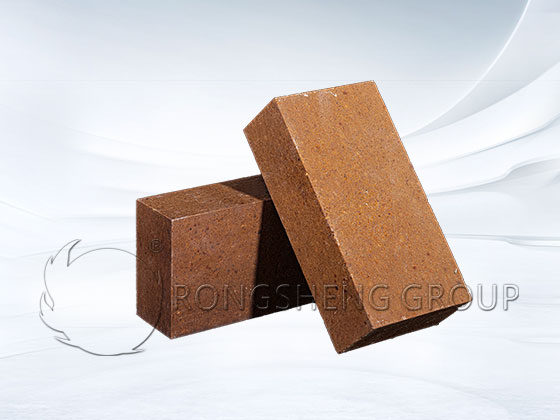
Rongsheng Magnesium Oxide Bricks for Sale
The corrosion resistance of alkaline refractories. Alkaline bricks have good corrosion resistance to metallurgical industry coal ash, light-burned dolomite, glass kiln melt, and ash. Different hot substances have different effects on the lining of alkaline bricks. In a strongly alkaline environment, such as the firing zone of a cement kiln, the order of corrosion resistance of lightly fired dolomite is magnesia dolomite brick > magnesia chrome brick > magnesia spinel brick. In steelmaking furnaces and electric furnace materials, CaO/SiO2 strong magnesia bricks are better than CaO/SiO2 low magnesia bricks. In the lattice body of the regenerator of the glass kiln, the magnesia brick with a low CaO/SiO2 ratio is better than the corresponding level of CaO/SiO2 strong magnesia brick. When producing stainless steel plates in an AOD furnace, the basicity of slag is lower than 2.2, and the thermal expansion of magnesia-chrome bricks is better than that of magnesia-dolomite bricks. The slag alkalinity exceeds 2.2, and the thermal expansion of magnesia dolomite bricks is better than that of magnesia chrome bricks. In heavy non-ferrous metallurgical furnaces, the level of resistance to FeO-SiO2 slag is magnesia-chrome bricks > magnesia bricks > magnesia spinel bricks > magnesia dolomite bricks.
Good sustained high-temperature performance. The refractoriness of basic refractory bricks is above 2000°C, which is significantly higher than other refractory bricks. The load softening temperature, continuous high-temperature flexural strength, continuous high-temperature volume stability, and high-temperature creep performance of each basic refractory brick increase with the increase of the density of the raw material for brick making, the reduction of the residue composition or the increase of the firing temperature. The softening temperature of general alkaline products is 1550~1600℃. High-end alkaline refractory products, such as magnesia dolomite bricks, magnesia spinel bricks, high-purity magnesia bricks, and directly bonded magnesia-chrome bricks, can be used at temperatures above 1700°C. Semi-recombined and recombined magnesia-chrome bricks can reach 1750-1800°C. The high-temperature flexural strength of each basic refractory brick decreases with the increase in the experimental temperature. The high-temperature flexural strength of rebonded magnesia-chrome bricks with high Cr2O3 content is relatively high.
The thermal expansion rate of alkaline refractory bricks is higher than other products. The thermal expansion rates of various basic refractory bricks with MgO as the main component are not much different. At 1600 °C, the linear expansion rate of magnesia bricks is relatively large, about 2.0%. High-end magnesia-chrome bricks have the lowest linear expansion rate of about 1.6%. In addition, the thermal expansion rate of basic refractory bricks is between the two.
The thermal conductivity of alkaline refractory bricks is higher than that of high alumina refractory bricks, clay bricks, and silicon carbide bricks. The thermal shock resistance of alkaline refractory bricks is not as good as that of clay bricks and high alumina refractory bricks. The thermal shock resistance of various basic refractory bricks decreases in the following order, magnesia spinel (magnesia-aluminum) bricks > magnesia-chrome bricks > magnesia-dolomite bricks > magnesia bricks.
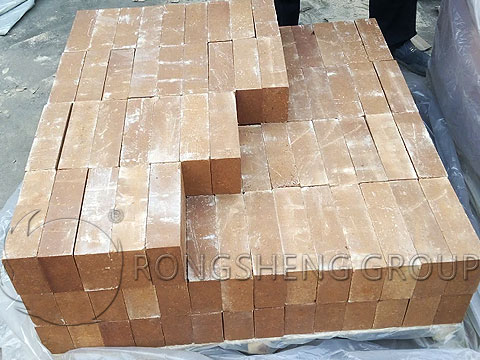
Technical indicators of magnesia bricks and magnesia silica bricks
Technical indicators of magnesia bricks and magnesia silica bricks. Magnesium bricks are alkaline refractory bricks made of magnesia. The content of magnesium oxide is more than 84%, and it can withstand the high temperature of about 2000 ° C. It is mainly used to build basic metallurgical furnaces. Magnesia-silicate bricks are also called high-silicon magnesia bricks. It refers to the magnesia refractory material with periclase as the main crystal phase and forsterite (2MgO·SiO2) as the second crystal phase (as the main binding phase).
Performance indicators of fused cast magnesia chrome bricks
Performance indicators of fused cast magnesia-chrome bricks. Fused-cast magnesia-chrome bricks are refractory products made from magnesia and chrome ore through electric melting and casting. Compared with magnesia bricks and chrome bricks, magnesia-chrome bricks have better thermal shock resistance, stable volume at high temperatures, and high load softening temperature.
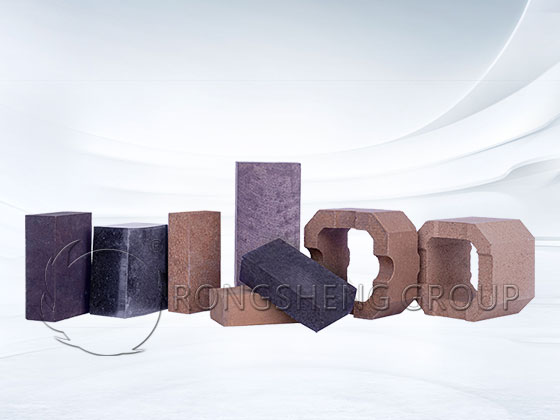
Rongsheng Kiln Refractory Manufacturer
As a manufacturer and seller of refractory lining materials for high-temperature kilns, Rongsheng kiln refractory manufacturers have a wealth of production, sales, and solutions for refractory lining materials. We can undertake the overall project of refractory lining and also provide refractory products for furnace refractory lining maintenance, such as T-3 magnesium brick 230*114*65 magnesium oxide bricks, etc. To purchase high-quality high-temperature kiln refractory lining materials and insulating materials, please contact us. We can provide free quotes and samples.
Leave Your Requirements on RS Kiln Refractory Bricks And Castable Materials! We Will Reply You In 12 Hours!: